Pour chaque installation de production ou d’entreposage, supprimer les temps d’arrêt des équipements (ou optimiser leur temps de disponibilité si vous préférez) reste l’un des facteurs déterminants.
Les bénéfices étant souvent tirés des derniers points de pourcentage de productivité, il est facile de comprendre les raisons d’un tel enjeu.
Que ce soit pour la maintenance de routine ou en raison de problèmes inattendus, les temps d’arrêt de plusieurs jours restent pourtant un problème courant dans de nombreuses installations.
Par ailleurs, effectuer les contrôles de sécurité éventuellement nécessaires sur les composants électriques sans arrêter une ligne entière peut être dangereux, voire impossible dans de nombreux cas. Les systèmes pneumatiques quant à eux nécessitent parfois l’intervention d’un technicien de maintenance spécialisé pour identifier l’origine d’une fuite ou d’un autre problème, réparer et préparer la remise en service du système.
L’importance de la maintenance, et en particulier de la maintenance préventive pour écarter les risques d’arrêt imprévu a souvent été soulignée et l’est encore aujourd’hui. Elle se concentre généralement sur des processus tels que la surveillance des conditions et l’analyse des causes profondes permettant d’identifier et de remplacer les composants défaillants avant qu’ils ne puissent provoquer un arrêt de la ligne.
Tout cela est bien beau, mais que se passerait-il si l’on pouvait supprimer les arrêts, même pour les entretiens de routine ?
Sur les grandes lignes manipulant de lourdes charges, un seul moteur entraîne traditionnellement de longues sections de convoyage. Tout se passe bien tant que le moteur fonctionne correctement. Mais que se passe-t-il lorsque ce moteur a besoin d’un entretien de routine ou qu’il tombe en panne de manière inattendue ?
Les principaux acteurs du secteur tels que Itoh Denki en sont conscients et ont développé des systèmes modulaires de rouleaux motorisés pour convoyeurs et déviateurs. En cas de problème, un rouleau moteur ou un module de déviation individuel peut simplement être retiré de la ligne et remplacé par une pièce de rechange. Cette dernière est rapidement reconfigurée, ce qui limite le temps d’arrêt. Les déviateurs ont été conçus pour être faciles à réparer, car ils fonctionnent généralement sur une alimentation 24 Vcc plutôt que sur une alimentation pneumatique. Le remplacement d’un moteur ou d’une courroie peut donc être effectué par un technicien interne et ne nécessite pas l’intervention d’un ingénieur spécialisé.
Utiliser des contrôleurs en réseau permet de récolter des données sur la consommation d’énergie et le cycle de vie des rouleaux motorisés en temps réel et ainsi d’effectuer une maintenance prédictive, de détecter et d’anticiper les défaillances imminentes.
Par ailleurs, la maintenance préventive sur ces systèmes n’est pratiquement plus nécessaire. Seules les reconfigurations ou les révisions majeures requièrent un arrêt de la ligne.
Les directeurs de site et responsables opérationnels qui cherchent à minimiser les temps d’arrêt et à rester compétitifs dans une conjoncture toujours plus difficile ont de quoi se réjouir.
Nos solutions vous intéressent ? Contactez-nous !
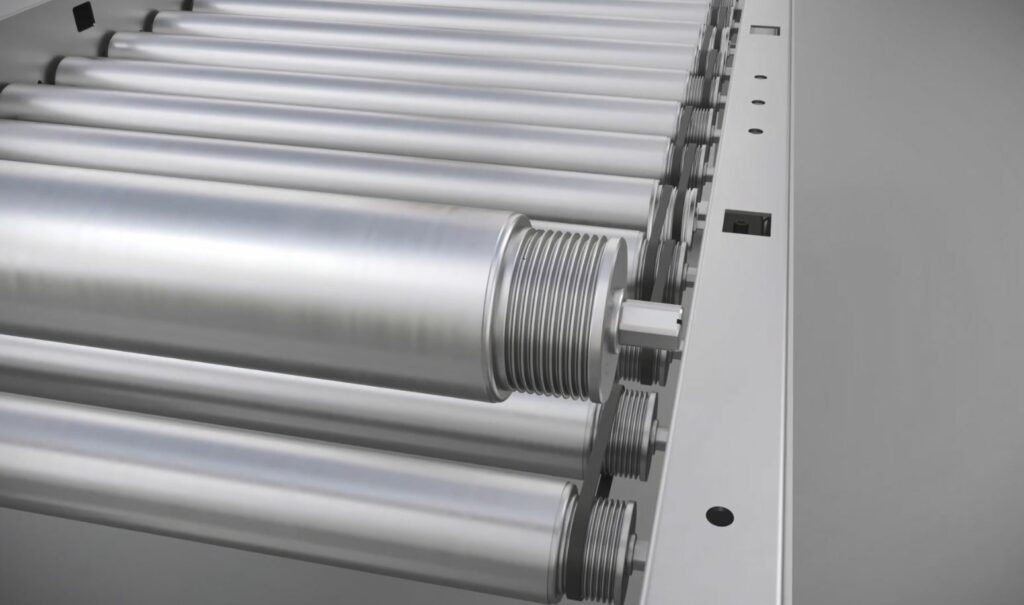