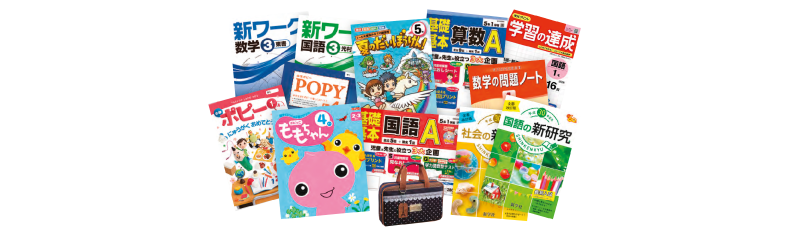
SITUATION : More references and more packages
In the situation where the number of material was increasing, Kusatsu Logistics Centre needed to handle a greater variety and amount of materials to pack, and increase its daily capacity from 25,000 to 30,000 boxes in peak season.
Moreover, educational materials became more diversified and frequently the delivery and packing form were changing, in consequence they couldn’t adapt their logistic to these evolutions.
BOTTLENECK
The bottleneck is the sorting process in the shipping which is operated manually, we couldn’t grasp rapidly the location of each tote and we couldn’t be flexible to possible order change or cancellations and mistakes were difficult and time-consuming to correct.
Boxes often got lost too.
So due to this sorting part,we simply could not increase production capacity.
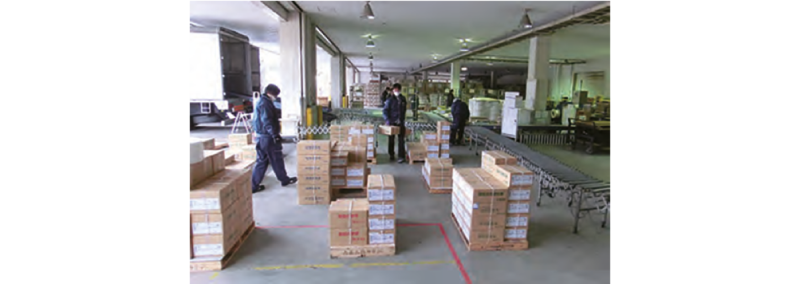
SOLUTION WITH CONVENTIONAL CONVEYOR ‘Heavy, Bulky, Long and Big’
When the company’s Executive Officer, Mr Nobuo Yamamoto, started looking for solutions, he found many ‘Heavy, Bulky, Long and Big’ solutions with a large sliding shoe sorter, etc. that required a long construction period with expansion of building, proposed from material handling makers.
But we couldn’t decide to go further with a big investment costing a lot of time and money.
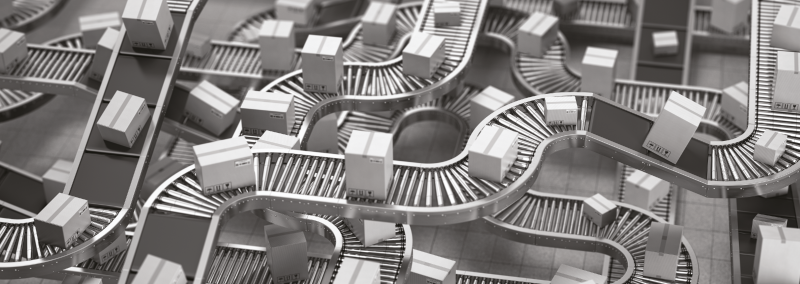
SOLUTION WITH idPAC : ‘Light, thin, short and small’
The improvement plan had reached a standstill, but it suddenly gained momentum when the manager in Kusatsu logistics dep. Mr. Matsui visited “Logis-Tech Tokyo 2016” to collect information and he was impressed by the compactness of idPAC, which was also a unique and completely opposite solution “Light, Thin, Short and Small”.
With idPAC, an optimal assembly line layout can be built freely and easily, he found that this solution would satisfy their condition of having a limited footprint.
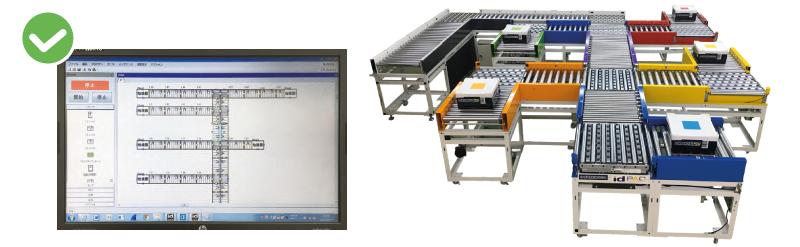
RESULTS : Sorting operation is fully automatized and staff is not required anymore
100% of mistakes were eliminated, less electricity was used and so on, and not only the sorting operation part but also other upstream and downstream parts were improved thanks to idPAC.
- Technical test was done before the installation, so 3-day installation was enough: half a day to uninstall and 2.5 days to install and test.
- Sorting staff is not required anymore the operation of transport companies are also streamlined.
- Electricity saving thanks to Run-on-demand functionality thanks to POWER MOLLER which only runs when necessary.
- Function to automatically stop totes just before they reach the extremity of the conveyor.
- No risk of crushing totes, with ZPA (the Zero Pressure Accumulation) function.
- With bar code reader, automated sorting by destination via barcode reader.
- Clean and silent: improved the working environment. Employees can sleep well without ringing noise in their ears.
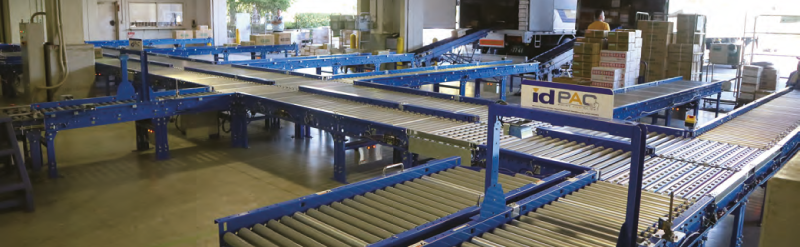
PERSPECTIVES : Applying the Effects of the idPAC to another center
Following the success story with idPAC, Mr Yamamoto sees opportunities for further implementations :
- Extend idPAC to upstream process (picking and packing area) soon.
- Increase loading lines by adding more branches in front of current lines.
- Increase transfer speed.
- Apply idPAC improvement on other sites of Shingakusha.
Now, it’s your turn to experience and make the most of idPAC !