At a time when energy prices remain at their highest levels for many years, plant managers will naturally be looking for any way possible to cut usage and therefore costs in this area.
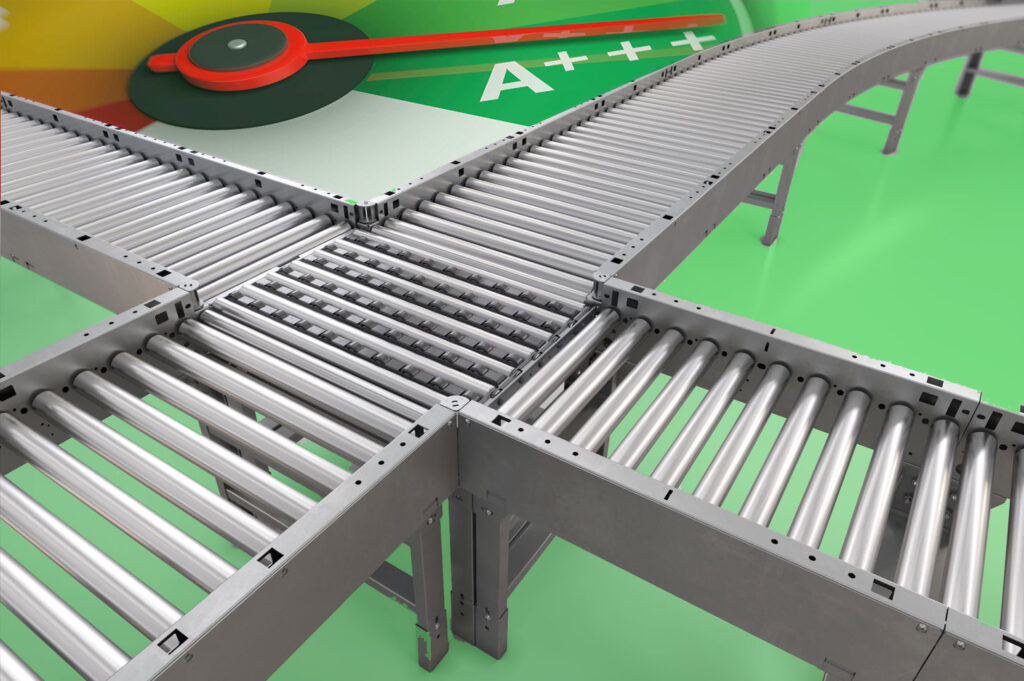
It may sometimes be difficult to cut energy use on existing on situ equipment – but when it comes to replacement or the installation of new production or handling systems, energy efficiency should be at the heart of every decision on design and specification.
This is especially true when it comes to conveyor lines paired with diverting and sortation equipment, given the substantial savings that are achievable through best practice in system design and selection.
On a line where the conveyor is a single length, then it must be moving whenever products are being sorted or diverted at any point along it, even if other sections of the conveyor are completely empty.
This usually means the presence of a large motor, from which significant power can end up being wasted if it is not running at premium efficiency.
However, thanks to the innovative work of manufacturers such as Itoh Denki, truly modular conveyor and sortation lines can now be created whose design can cut energy consumption by up to 60 per cent when compared with traditional alternatives.
How ? Put simply, the conveyor line is divided into multiple sections, each driven by an individual motor driven roller or a diverter for the lateral transfers. If there is a large accumulation of packages at one end of the line, but the rest is empty, then the rollers and diverters in the empty sections will remain idle until they are needed again.
In short, only the sections that are conveying a parcel at any one time are actually in motion – meaning no more energy is used than is actually needed.
Finally, the presence of double bearings on the motor driven rollers on modular systems has been shown to result in significantly less friction and heat from operation, meaning a higher proportion of the supplied power is directed to actually moving the rollers.
These modular designs all run off standard 24V DC power, rather than three-phase power or pneumatics, as is typically the case with traditional conveyor lines – this itself creates further savings as lower maintenance is typically needed on 24V DC systems when compared with the specialist maintenance needed to ensure pneumatic systems operate safely and efficiently.
Next time you are seeking to replace or specify a new conveyor system, think carefully about your design – and ensure it delivers optimal performance and maximum energy efficiency.